Az INES francia napenergia intézet új PV modulokat fejlesztett ki hőre lágyuló műanyagokból és Európában beszerzett természetes szálakból, például lenből és bazaltból.A tudósok célja, hogy csökkentsék a napelemek környezeti lábnyomát és súlyát, miközben javítják az újrahasznosítást.
Elől újrahasznosított üveglap, hátul vászon kompozit
Kép: GD
A pv magazin Franciaországból
A francia Nemzeti Napenergia Intézet (INES) – a francia Alternatív Energiák és Atomenergia Bizottság (CEA) részlege – kutatói olyan napelem modulokat fejlesztenek, amelyek elülső és hátsó oldalán új, bioalapú anyagokat tartalmaznak.
„Mivel a szénlábnyom és az életciklus-elemzés mára a fotovoltaikus panelek kiválasztásának alapvető kritériumává vált, az anyagok beszerzése a következő években kulcsfontosságú elem lesz Európában” – mondta Anis Fouini, a CEA-INES igazgatója. , a France pv magazinnak adott interjújában.
Aude Derrier, a kutatási projekt koordinátora elmondta, hogy kollégái megvizsgálták a már létező különféle anyagokat, hogy megtalálják azt, amely lehetővé tenné a modulgyártók számára, hogy olyan paneleket állítsanak elő, amelyek javítják a teljesítményt, a tartósságot és a költségeket, miközben csökkentik a környezeti hatást.Az első bemutató egy teljesen kompozit anyagba integrált heterojunkciós (HTJ) napelemekből áll.
"Az elülső oldal üvegszállal töltött polimerből készült, ami átlátszóságot biztosít" - mondta Derrier."A hátsó oldal hőre lágyuló műanyag alapú kompozitból készült, amelybe két szál, a len és a bazalt szövését integrálták, ami mechanikai szilárdságot, de jobb nedvességállóságot is biztosít."
A len Észak-Franciaországból származik, ahol a teljes ipari ökoszisztéma már jelen van.A bazaltot Európából szerzik be, és az INES ipari partnere szövi.Ez wattonként 75 gramm szén-dioxid-kibocsátással csökkentette az azonos teljesítményű referenciamodulhoz képest.A súlyt is optimalizálták, és kevesebb mint 5 kilogramm négyzetméterenként.
„Ez a modul a tetőtéri napelemek és az épületek integrációját célozza” – mondta Derrier.„Az előnye, hogy természetesen fekete színű, nincs szükség hátlapra.Az újrahasznosítás szempontjából az újraolvasztható hőre lágyuló műanyagoknak köszönhetően a rétegek szétválasztása technikailag is egyszerűbb.”
A modul a jelenlegi folyamatok adaptálása nélkül is elkészíthető.Derrier szerint az ötlet az, hogy a technológiát további beruházások nélkül átadják a gyártóknak.
„Az egyetlen elengedhetetlen feltétel az, hogy legyen fagyasztószekrény az anyag tárolására, és ne kezdjük meg a gyanta térhálósítási folyamatát, de a legtöbb gyártó manapság prepreget használ, és már fel vannak szerelve erre” – mondta.
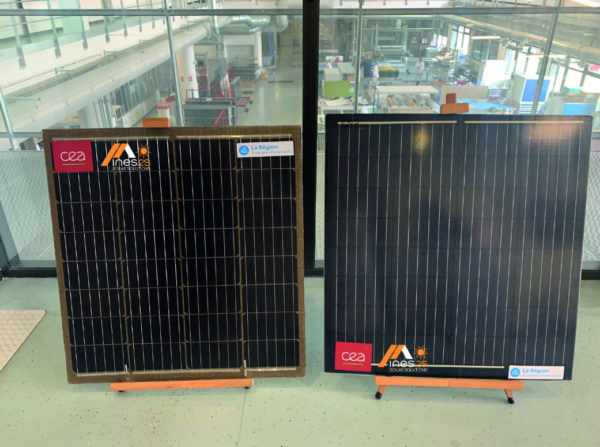
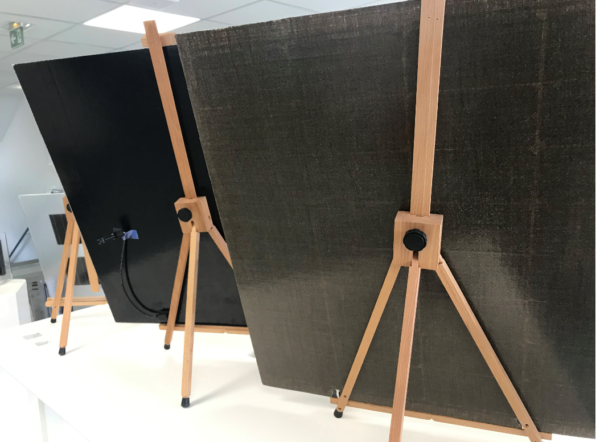
„Az üveg második életén dolgoztunk, és kifejlesztettünk egy modult, amely újrafelhasznált 2,8 mm-es üvegből áll, amely egy régi modulból származik” – mondta Derrier.„Használtunk hőre lágyuló kapszulázót is, amely nem igényel térhálósítást, így könnyen újrahasznosítható, valamint lenszálas hőre lágyuló kompozitot az ellenállás érdekében.”
A modul bazaltmentes hátsó felülete natúr vászon színű, ami esztétikailag érdekes lehet az építészek számára például homlokzati integráció szempontjából.Ezenkívül az INES számítási eszköz 10%-kal csökkentette a szénlábnyomot.
„Most feltétlenül meg kell kérdőjelezni a fotovoltaikus ellátási láncokat” – mondta Jouini.„A Nemzetközi Fejlesztési Terv keretében a Rhône-Alpes régió segítségével ezért a szoláris szektoron kívüli szereplőket kerestünk, hogy új hőre lágyuló műanyagokat és új szálakat találjunk.Gondoltunk a jelenlegi laminálási folyamatra is, ami nagyon energiaigényes.”
A nyomás alá helyezés, a préselés és a hűtési fázis között a laminálás általában 30-35 percig tart, 150-160 C körüli üzemi hőmérséklet mellett.
„De azoknál a moduloknál, amelyek egyre gyakrabban tartalmaznak környezetbarát anyagokat, a hőre lágyuló műanyagokat körülbelül 200 C-ról 250 C-ra kell átalakítani, tudván, hogy a HTJ technológia érzékeny a hőre, és nem haladhatja meg a 200 C-ot” – mondta Derrier.
A kutatóintézet a franciaországi székhelyű indukciós hőkompressziós specialistával, a Roctool-lal együttműködve csökkenti a ciklusidőt, és az ügyfelek igényei szerint alakítja ki a formákat.Közösen kifejlesztettek egy polipropilén típusú hőre lágyuló kompozitból készült hátsó felületű modult, amelybe újrahasznosított szénszálakat integráltak.Az elülső oldal hőre lágyuló műanyagból és üvegszálból készült.
"A Roctool indukciós hőkompressziós eljárása lehetővé teszi a két első és hátsó lemez gyors felmelegítését anélkül, hogy a HTJ cellák magjában el kellene érni a 200 C-ot" - mondta Derrier.
A vállalat azt állítja, hogy a beruházás alacsonyabb, és a folyamat mindössze néhány perces ciklusidőt érhet el, miközben kevesebb energiát használ.A technológia a kompozit gyártókat célozza meg, hogy lehetővé tegye számukra különböző formájú és méretű alkatrészek gyártását, miközben könnyebb és tartósabb anyagokat integrálnak.
Feladás időpontja: 2022. június 24