Az Ines Francia Napenergia Intézet új PV modulokat fejlesztett ki Európában, például a lenben és a bazaltban beszerzett hőre lágyuló műanyagokkal és természeti szálakkal. A tudósok célja, hogy csökkentsék a napelemek környezeti lábnyomát és súlyát, miközben javítják az újrahasznosítást.
Egy újrahasznosított üvegpanel az elülső oldalon és egy vászon kompozit a hátulon
Kép: GD
A PV magazin Franciaországból
A francia Nemzeti Napenergia Intézet (INES) kutatói-a francia alternatív energiák és az Atomenergia Bizottság (CEA) részlege-olyan napenergia-modulokat fejlesztenek ki, amelyek új bio-alapú anyagokat tartalmaznak az első és a hátsó oldalon.
"Mivel a szénlábnyom és az életciklus-elemzés most alapvető kritériumokká vált a fotovoltaikus panelek megválasztásában, az anyagok beszerzése Európában döntő elem lesz az elkövetkező néhány évben"-mondta Anis Fouini, a CEA-INS igazgatója, a CEA-INS igazgatója. , egy interjúban a PV magazin Franciaországgal.
Aude Derrier, a kutatási projekt koordinátora elmondta, hogy kollégái megvizsgálták a már létező különféle anyagokat, hogy megtalálják azt, amely lehetővé teszi a modulgyártók számára, hogy olyan paneleket készítsenek, amelyek javítják a teljesítményt, a tartósságot és a költségeket, miközben csökkentik a környezeti hatást. Az első demonstrátor heterojunction (HTJ) napelemekből áll, amelyeket egy all-kompozit anyagba integráltak.
"Az elülső oldal üvegszálas töltött polimerből készül, amely átláthatóságot biztosít"-mondta Derrier. "A hátsó oldal kompozitból készül, olyan hőre lágyuló műanyagok alapján, amelyekbe két szál, a len és a bazalt szövése integrálódott, amelyek mechanikai szilárdságot biztosítanak, de jobb páratartalom ellenállását is biztosítják."
A len észak -Franciaországból származik, ahol a teljes ipari ökoszisztéma már jelen van. A bazalt Európában másutt származik, és az Ines ipari partnere szőtt. Ez csökkentette a szénlábnyomot 75 gramm CO2 -vel wattonként, összehasonlítva az azonos teljesítményű referencia modullal. A súlyt szintén optimalizálták, és kevesebb, mint 5 kilogramm / négyzetméter.
"Ez a modul a tetőtéri PV -re és az épület integrációjára irányul" - mondta Derrier. „Ennek előnye az, hogy természetesen fekete színű, anélkül, hogy vissza kellene adni. Az újrahasznosítás szempontjából, a hőre lágyuló műanyagnak köszönhetően, amelyet át lehet alakítani, a rétegek elválasztása technikailag egyszerűbb. ”
A modul az aktuális folyamatok adaptálása nélkül készíthető. Derrier elmondta, hogy az ötlet az, hogy a technológiát a gyártóknak továbbítsák, további beruházások nélkül.
"Az egyetlen kötelező, ha fagyasztók vannak az anyag tárolására, és nem a gyanta térhálósítási folyamatának megkezdésére, de a legtöbb gyártó manapság a Prepreg-t használja, és erre már felkészült"-mondta.
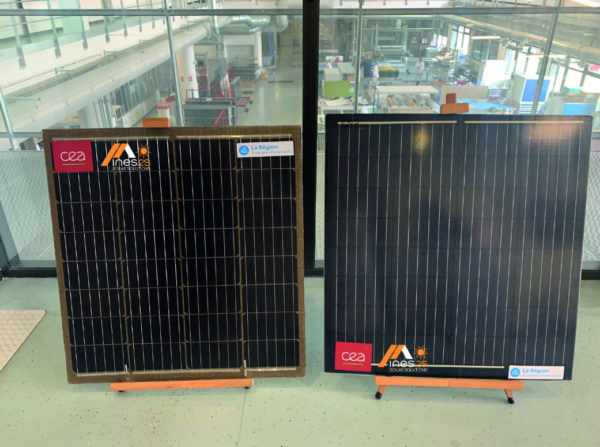
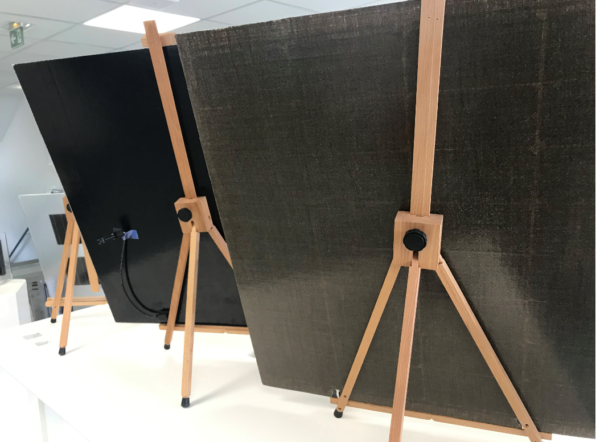
"Dolgoztunk az üveg második életén, és kifejlesztettünk egy olyan modulot, amely egy régi modulból származó, újrafelhasználott 2,8 mm -es üvegből áll" - mondta Derrier. "Olyan hőre lágyuló kapszulant is használtunk, amely nem igényel keresztkötést, amelyet ezért könnyű újrahasznosítani, és az ellenállás lenszálas hőre lágyuló kompozitja."
A modul bazaltmentes hátsó felülete természetes vászon színű, amely például az építészek számára esztétikai szempontból érdekes lehet például a homlokzat integrációja szempontjából. Ezenkívül az INES számítási eszköz 10% -kal csökkent a szénlábnyomban.
"Most elengedhetetlen a fotovoltaikus ellátási láncok megkérdőjelezése" - mondta Jouini. „A Rhône-Alpes régió segítségével a Nemzetközi Fejlesztési Terv keretein belül a napenergia-ágazaton kívüli játékosokat kerestük új hőre lágyuló műanyagok és új szálak megtalálására. Arra is gondolkodtunk a jelenlegi laminálási folyamaton, amely nagyon energiabeusinziós. ”
A nyomás, a préselés és a hűtési fázis között a laminálás általában 30 és 35 perc között tart, üzemi hőmérséklete körülbelül 150 ° C - 160 ° C.
"De az olyan modulok esetében, amelyek egyre inkább beépítik az öko-tervezett anyagokat, 200 ° C-tól 250 ° C-ig kell átalakítani a hőre lágyuló műanyagokat, tudva, hogy a HTJ technológia érzékeny a hőre, és nem haladhatja meg a 200 ° C-ot"-mondta Derrier.
A Kutatóintézet a franciaországi székhelyű indukciós termocompressziós szakemberrel, a Roctool-nal együttműködik, hogy csökkentse a ciklusidőket és formákat készítsen az ügyfelek igényeinek megfelelően. Együtt kifejlesztettek egy modult, amelynek hátsó arca polipropilén típusú hőre lágyuló kompozitból készült, amelybe újrahasznosított szénszálak integrálódtak. Az elülső oldal hőre lágyuló és üvegszálból készül.
"A Roctool indukciós termocompressziós folyamata lehetővé teszi a két elülső és hátsó lemez gyors fűtését anélkül, hogy a HTJ sejtek középpontjában 200 ° C -ot kellene elérnie" - mondta Derrier.
A társaság azt állítja, hogy a beruházás alacsonyabb, és a folyamat csak néhány perces ciklusidőt érhet el, miközben kevesebb energiát használ. A technológia célja a kompozit gyártók, hogy lehetőséget biztosítsanak számukra különböző formájú és méretű részek előállítására, miközben a könnyebb és tartósabb anyagokat integrálják.
A postai idő: június-24-2022